In recent years, thanks to the rapid development of the new energy industry, laser welding has rapidly penetrated the entire new energy industry due to its fast and stable advantages. Among them, laser welding equipment accounts for the highest proportion of applications in the entire new energy industry.
Laser welding has quickly become the first choice in all walks of life due to its fast speed, large depth, and small deformation. From spot welds to butt welds, build-up and seal welds, laser welding provides unparalleled precision and control. It plays an important role in industrial production and manufacturing, including military industry, medical care, aerospace, 3C auto parts, mechanical sheet metal, new energy and other industries.
Compared with other welding technologies, laser welding has its unique advantages and disadvantages.
Advantage:
1. Fast speed, large depth and small deformation.
2. Welding can be performed at normal temperature or under special conditions, and the welding equipment is simple. For example, a laser beam does not drift in an electromagnetic field. Lasers can weld in a vacuum, air or certain gas environments, and can weld materials that are through glass or transparent to the laser beam.
3. It can weld refractory materials such as titanium and quartz, and can also weld dissimilar materials with good results.
4. After the laser is focused, the power density is high. The aspect ratio can reach 5:1, and can reach up to 10:1 when welding high-power devices.
5. Micro welding can be performed. After the laser beam is focused, a small spot can be obtained and can be positioned accurately. It can be applied to the assembly and welding of micro and small workpieces to achieve automated mass production.
6. It can weld hard-to-reach areas and perform non-contact long-distance welding, with great flexibility. Especially in recent years, YAG laser processing technology has adopted optical fiber transmission technology, which has enabled laser welding technology to be more widely promoted and applied.
7. The laser beam is easy to split in time and space, and multiple beams can be processed at multiple locations simultaneously, providing conditions for more precise welding.
Defect:
1. The assembly accuracy of the workpiece is required to be high, and the position of the beam on the workpiece cannot be significantly deviated. This is because the laser spot size after focusing is small and the weld seam is narrow, making it difficult to add filler metal materials. If the assembly accuracy of the workpiece or the positioning accuracy of the beam does not meet the requirements, welding defects are prone to occur.
2. The cost of lasers and related systems is high, and the one-time investment is large.
Common laser welding defects in lithium battery manufacturing
1. Welding porosity
Common defects in laser welding are pores. The welding molten pool is deep and narrow. During the laser welding process, nitrogen invades the molten pool from the outside. During the cooling and solidification process of the metal, the solubility of nitrogen decreases with the decrease of temperature. When the molten pool metal cools to start to crystallize, , the solubility will drop sharply and suddenly. At this time, a large amount of gas will precipitate to form bubbles. If the floating speed of the bubbles is less than the metal crystallization speed, pores will be generated.
In applications in the lithium battery industry, we often find that pores are particularly likely to occur during the welding of the positive electrode, but rarely occur during the welding of the negative electrode. This is because the positive electrode is made of aluminum and the negative electrode is made of copper. During welding, the liquid aluminum on the surface has condensed before the internal gas completely overflows, preventing the gas from overflowing and forming large and small holes. Small stomata.
In addition to the causes of pores mentioned above, pores also include outdoor air, moisture, surface oil, etc. In addition, the direction and angle of nitrogen blowing will also affect the formation of pores.
As for how to reduce the occurrence of welding pores?
First, before welding, the oil stains and impurities on the surface of the incoming materials need to be cleaned in time; in the production of lithium batteries, incoming material inspection is an essential process.
Second, the shielding gas flow should be adjusted according to factors such as welding speed, power, position, etc., and should be neither too large nor too small. The protective cloak pressure should be adjusted according to factors such as laser power and focus position, and should be neither too high nor too low. The shape of the protective cloak nozzle should be adjusted according to the shape, direction and other factors of the weld so that the protective cloak can evenly cover the welding area.
Third, control the temperature, humidity and dust in the air in the workshop. The ambient temperature and humidity will affect the moisture content on the surface of the substrate and the protective gas, which will in turn affect the generation and escape of water vapor in the molten pool. If the ambient temperature and humidity are too high, there will be too much moisture on the surface of the substrate and the protective gas, generating a large amount of water vapor, resulting in pores. If the ambient temperature and humidity are too low, there will be too little moisture on the surface of the substrate and in the shielding gas, reducing the generation of water vapor, thereby reducing pores; let the quality personnel detect the target value of temperature, humidity and dust at the welding station.
Fourth, the beam swing method is used to reduce or eliminate pores in laser deep penetration welding. Due to the addition of swing during welding, the reciprocating swing of the beam to the weld seam causes repeated remelting of part of the weld seam, which prolongs the residence time of the liquid metal in the welding pool. At the same time, the deflection of the beam also increases the heat input per unit area. The depth-to-width ratio of the weld is reduced, which is conducive to the emergence of bubbles, thereby eliminating pores. On the other hand, the swing of the beam causes the small hole to swing accordingly, which can also provide a stirring force for the welding pool, increase the convection and stirring of the welding pool, and have a beneficial effect on eliminating the pores.
Fifth, the pulse frequency, the pulse frequency refers to the number of pulses emitted by the laser beam per unit time, which will affect the heat input and heat accumulation in the molten pool, and then affect the temperature field and flow field in the molten pool. If the pulse frequency is too high, it will lead to excessive heat input in the molten pool, causing the temperature of the molten pool to be too high, producing metal vapor or other elements that are volatile at high temperatures, resulting in pores. If the pulse frequency is too low, it will lead to insufficient heat accumulation in the molten pool, causing the temperature of the molten pool to be too low, reducing the dissolution and escape of gas, resulting in pores. Generally speaking, the pulse frequency should be chosen within a reasonable range based on substrate thickness and laser power, and avoid being too high or too low.
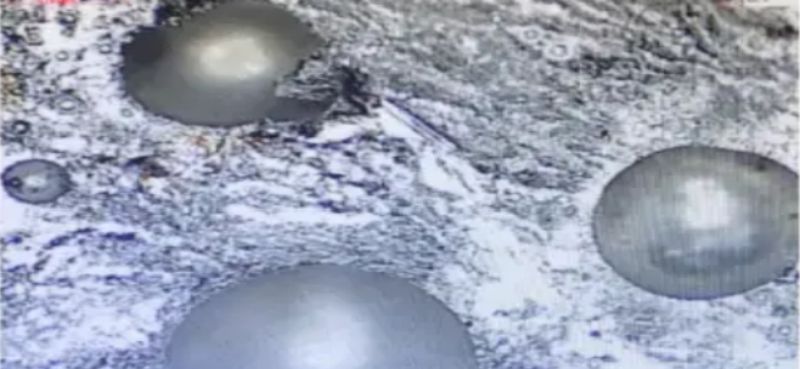
Welding holes (laser welding)
2. Weld spatter
The spatter generated during the welding process, laser welding will seriously affect the surface quality of the weld, and will pollute and damage the lens. The general performance is as follows: after laser welding is completed, many metal particles appear on the surface of the material or workpiece and adhere to the surface of the material or workpiece. The most intuitive performance is that when welding in the mode of the galvanometer, after a period of use of the protective lens of the galvanometer, there will be dense pits on the surface, and these pits are caused by welding spatter. After a long time, it is easy to block the light, and there will be problems with welding light, resulting in a series of problems such as broken welding and virtual welding.
What are the causes of splashing?
First, the power density, the greater the power density, the easier it is to generate spatter, and the spatter is directly related to the power density. This is a century-old problem. At least so far, the industry has been unable to solve the problem of splashing, and can only say that it has been slightly reduced. In the lithium battery industry, splashing is the biggest culprit of battery short circuit, but it has not been able to solve the root cause. The impact of spatter on the battery can only be reduced from the point of view of protection. For example, a circle of dust removal ports and protective covers are added around the welding part, and rows of air knives are added in circles to prevent the impact of spatter or even damage to the battery. Destroying the environment, products and components around the welding station can be said to have exhausted the means.
As for solving the spatter problem, it can only be said that reducing the welding energy helps to reduce spatter. Reducing the welding speed can also help if penetration is insufficient. But in some special process requirements, it has little effect. It is the same process, different machines and different batches of materials have completely different welding effects. Therefore, there is an unwritten rule in the new energy industry, one set of welding parameters for one piece of equipment.
Second, if the surface of the processed material or workpiece is not cleaned, oil stains or pollutants will also cause serious splashes. At this time, the easiest thing is to clean the surface of the processed material.
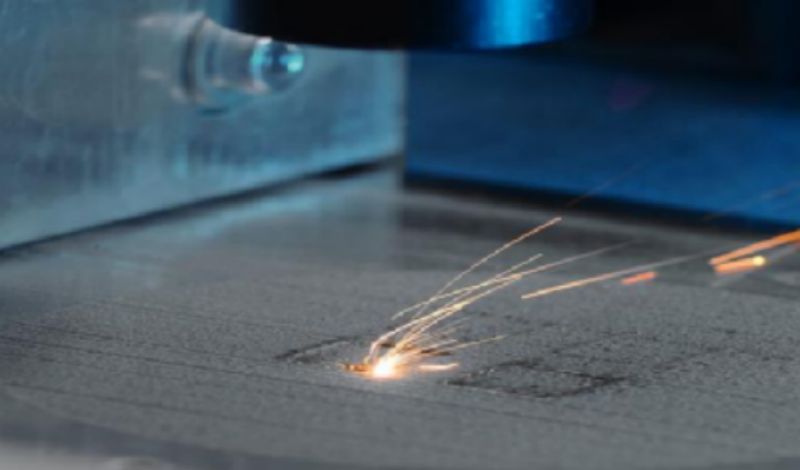
3. High reflectivity of laser welding
Generally speaking, high reflection refers to the fact that the processing material has a small resistivity, a relatively smooth surface, and a low absorption rate for near-infrared lasers, which leads to a large amount of laser emission, and because most lasers are used in vertical Due to the material or a small amount of inclination, the returning laser light re-enters the output head, and even part of the returning light is coupled into the energy-transmitting fiber, and is transmitted back along the fiber to the inside of the laser, making the core components inside the laser continue to be at high temperature.
When the reflectivity is too high during laser welding, the following solutions can be taken:
3.1 Use anti-reflection coating or treat the surface of the material: coating the surface of the welding material with an anti-reflection coating can effectively reduce the reflectivity of the laser. This coating is usually a special optical material with low reflectivity that absorbs laser energy instead of reflecting it back. In some processes, such as current collector welding, soft connection, etc., the surface can also be embossed.
3.2 Adjust the welding angle: By adjusting the welding angle, the laser beam can be incident on the welding material at a more appropriate angle and reduce the occurrence of reflection. Normally, having the laser beam incident perpendicularly to the surface of the material to be welded is a good way to reduce reflections.
3.3 Adding auxiliary absorbent: During the welding process, a certain amount of auxiliary absorbent, such as powder or liquid, is added to the weld. These absorbers absorb laser energy and reduce reflectivity. The appropriate absorbent needs to be selected based on the specific welding materials and application scenarios. In the lithium battery industry, this is unlikely.
3.4 Use optical fiber to transmit laser: If possible, optical fiber can be used to transmit laser to the welding position to reduce reflectivity. Optical fibers can guide the laser beam to the welding area to avoid direct exposure to the surface of the welding material and reduce the occurrence of reflections.
3.5 Adjusting laser parameters: By adjusting parameters such as laser power, focal length, and focal diameter, the distribution of laser energy can be controlled and reflections can be reduced. For some reflective materials, reducing laser power may be an effective way to reduce reflections.
3.6 Use a beam splitter: A beam splitter can guide part of the laser energy into the absorption device, thereby reducing the occurrence of reflections. Beam splitting devices usually consist of optical components and absorbers, and by selecting appropriate components and adjusting the layout of the device, lower reflectivity can be achieved.
4. Welding undercut
In the lithium battery manufacturing process, which processes are more likely to cause undercutting? Why does undercutting occur? Let's analyze it.
Undercut, generally the welding raw materials are not well combined with each other, the gap is too large or the groove appears, the depth and width are basically greater than 0.5mm, the total length is greater than 10% of the weld length, or greater than the product process standard the requested length.
In the whole lithium battery manufacturing process, undercutting is more likely to occur, and it is generally distributed in the sealing pre-welding and welding of the cylindrical cover plate and the sealing pre-welding and welding of the square aluminum shell cover plate. The main reason is that the sealing cover plate needs to cooperate with the shell to Welding, the matching process between the sealing cover plate and the shell is prone to excessive weld gaps, grooves, collapse, etc., so it is particularly prone to undercuts.
So what causes undercutting?
If the welding speed is too fast, the liquid metal behind the small hole pointing to the center of the weld will not have time to redistribute, resulting in solidification and undercutting on both sides of the weld. In view of the above situation, we need to optimize the welding parameters. To put it simply, it is repeated experiments to verify various parameters, and keep doing DOE until the appropriate parameters are found.
2. Excessive weld gaps, grooves, collapses, etc. of welding materials will reduce the amount of molten metal filling the gaps, making undercuts more likely to occur. This is a question of equipment and raw materials. Whether the welding raw materials meet the incoming material requirements of our process, whether the equipment accuracy meets the requirements, etc. The normal practice is to constantly torture and beat the suppliers and the people in charge of the equipment.
3. If the energy drops too fast at the end of laser welding, the small hole may collapse, resulting in local undercutting. The correct matching of power and speed can effectively prevent the formation of undercuts. As the old saying goes, repeat experiments, verify various parameters, and continue DOE until you find the right parameters.
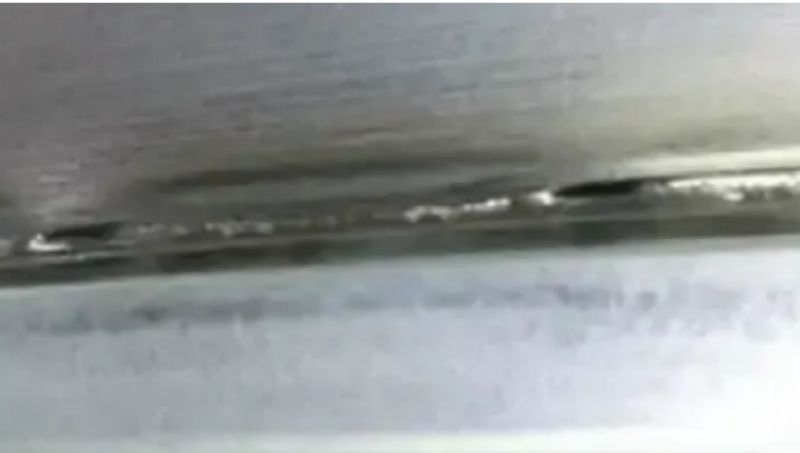
5. Weld center collapse
If the welding speed is slow, the molten pool will be larger and wider, increasing the amount of molten metal. This can make maintaining surface tension difficult. When the molten metal becomes too heavy, the center of the weld may sink and form dips and pits. In this case, the energy density needs to be appropriately reduced to prevent melt pool collapse.
In another situation, the welding gap just forms a collapse without causing perforation. This is undoubtedly a problem of equipment press fit.
A proper understanding of the defects that can occur during laser welding and the causes of different defects allows for a more targeted approach to resolve any abnormal welding problems.
6. Weld cracks
The cracks that appear during continuous laser welding are mainly thermal cracks, such as crystal cracks and liquefaction cracks. The main cause of these cracks is the large shrinkage forces generated by the weld before it completely solidifies.
There are also the following reasons for cracks in laser welding:
1. Unreasonable weld design: Improper design of the geometry and size of the weld may cause welding stress concentration, thereby causing cracks. The solution is to optimize the weld design to avoid welding stress concentration. You can use appropriate offset welds, change the weld shape, etc.
2. Mismatch of welding parameters: Improper selection of welding parameters, such as too fast welding speed, too high power, etc., may lead to uneven temperature changes in the welding area, resulting in large welding stress and cracks. The solution is to adjust the welding parameters to match the specific material and welding conditions.
3. Poor preparation of the welding surface: Failure to properly clean and pre-treat the welding surface before welding, such as removing oxides, grease, etc., will affect the quality and strength of the weld and easily lead to cracks. The solution is to adequately clean and pre-treat the welding surface to ensure that impurities and contaminants in the welding area are effectively treated.
4. Improper control of welding heat input: Poor control of heat input during welding, such as excessive temperature during welding, improper cooling rate of the welding layer, etc., will lead to changes in the structure of the welding area, resulting in cracks. The solution is to control the temperature and cooling rate during welding to avoid overheating and rapid cooling.
5. Insufficient stress relief: Insufficient stress relief treatment after welding will result in insufficient stress relief in the welded area, which will easily lead to cracks. The solution is to perform appropriate stress relief treatment after welding, such as heat treatment or vibration treatment (main reason).
As for the manufacturing process of lithium batteries, which processes are more likely to cause cracks?
Generally, cracks are prone to occur during sealing welding, such as sealing welding of cylindrical steel shells or aluminum shells, sealing welding of square aluminum shells, etc. In addition, during the module packaging process, the welding of the current collector is also prone to cracks.
Of course, we can also use filler wire, preheating or other methods to reduce or eliminate these cracks.
Post time: Sep-01-2023